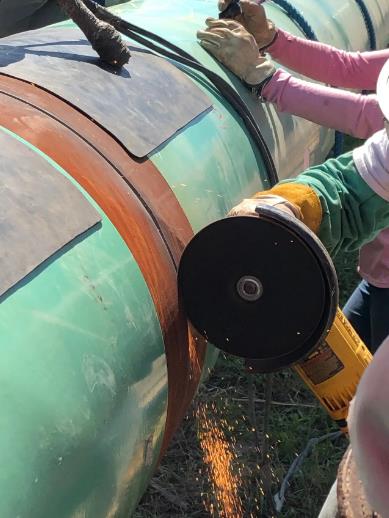
Tips for increasing safty and productivity when using resinoid-bonded cutting and grinding wheel
Whether using a cutting, grinding or combination wheel, safety is always a top priority. Safety is everyone’s responsibility, which means always keeping the guard on the tool, using cutting wheels for cutting and not grinding, resisting physically hitting the edge of a wheel to break it in and make it more aggressive and ensuring the RPM of the wheel is always higher than the RPM rating of the tool to make sure to not over-speed the wheel. Operators who practice these good habits can decrease the chance of accidents and increase productivity.
“It’s important to stay focused on safety when the location is a challenge – cutting and grinding overhead, laying down on the ground, working in a smaller space where there are constraints are all times when there are opportunities to take short cuts that compromise safety,” says Tony, category manager, Ryli Abrasives. “It’s easy to forget about some of the safety requirements when you believe the guard is getting in the way or you are having trouble with an application. Make sure you are using the proper tool and abrasive for the application, and you aren’t modifying them in a way that’s unsafe.”
Because of labor shortages, everyone is trying to do more with less while still maintaining or increasing productivity. Consider these tips and techniques to follow for improving safety and productivity when it comes to using cutting, grinding and combination wheels.
CUTTING STYLE
In addition to matching the right abrasive to the tool, application and material, the operator’s style in using the proper angle and amount of pressure plays a role in successful use of thin cutting wheels.
“As you present the cutting wheel perpendicular to the work surface, the tendency is to push straight down as hard as you can because you think it will achieve a faster removal rate,” Tony says. “But you can maximize the life of the wheel without sacrificing speed with a different technique. By adding a slight forward and back motion and applying a moderate amount of pressure, you can feel your way through the cut. This allows the wheel to break down and expose the right amount of fresh grain, maximizing efficiency and minimizing waste.”
“Most times, if you press really hard and just push through the workpiece, you’re going to generate a lot of heat, which is the enemy of most abrasives,” he adds. “You can end up actually pushing through molten metal rather than cutting through metal, which will slow your progress and wear the wheel down excessively or cause it to glaze and reduce cutting speed.”
Thin resinoid-bonded cutting wheels are made and reinforced to work vertically. They are not designed to the work at angles or to bend in the cut.
“I have often witnessed cutting wheels being used for ‘feathering,’ which is where you lightly grind a weld to smooth out the surface or blend the starts and stops,” Tony says. “Cutting wheels are not designed for this because the reinforcements support vertical pressure. Feathering is not something that is safe over the long term. You may get away with for a while but eventually that wheel is going to break or become compromised, especially if you put too much pressure on it from a side load standpoint.”
Also, operators should always enter the cut from the point of least resistance, which is the most efficient place to begin cutting. When cutting corners or square profiles, this means entering from the corner for the least amount of surface contact to start the cut and allow the cleanest penetration.
Finally, some operators have confusion regarding Type 1 and Type 27 cutting wheels. Type 1 wheels are flat and Type 27 wheels, often referred to as a depressed center wheel, have a raised hub at the center.
The Type 27 wheel is designed to allow for additional offset or clearance between the wheel and the tool. However, it reduces the amount of cutting surface and the raised hub can also cause interference, especially when the operator is cutting thicker material or plunging the wheel too deeply into the workpiece.
“One thing you have to look for is the depth when cutting with a Type 27 wheel because you can cut into the depressed center of the wheel without even knowing it until the wheel breaks,” Tony says. “With the raised hub, you need to make sure that that depth isn’t too deep as to where the workpiece grinds into the raised hub. Make sure there is no interference. If you pull out your wheel and there are cut marks on the hub, stop and review the application for safety and consider a Type 1 wheel.”
GRINDING ADVICE
Type 27 grinding wheels can be used at a multitude of angles and one bit of good advice for operators is to pull before they push.
“Most brand-new grinding wheels are very aggressive from the start,” Tony says. “If you start with a pull motion instead of a push motion, you greatly reduce the chance of gouging the workpiece. Gouging can be costly if it’s too deep because of time-consuming repairs or having to scrap expensive workpiece material.”
“Then, using a long, consistent motion throughout can certainly help with the ergonomics,” he continues, “by allowing the wheel to do the work without too much pressure so that you maintain control over the grinder. You’re not just leaning down on it as hard as you can.”
As with cutting wheels, another issue with grinding wheels is glazing, where the grinding wheel quits breaking down and exposing fresh abrasive to maintain cut rate. The abrasive stops working efficiently and has a shiny or smooth appearance. Choosing the right abrasive combination, including the correct grain type, grit size and wheel hardness specific for the application, helps prevents glazing from occurring and allows the abrasive to do the work.
COMBINATION SOLUTIONS
As an alternative to cutting and grinding wheels, combination wheels can solve a lot of issues for specific applications.
“It’s very important that you pay attention to the manufacturer markings on the wheel that indicate if that wheel is only to be used vertically for applications like notching or if it can also be used at an angle like a grinding wheel,” Tony says. “Not all combination wheels are created equal. Understand the capabilities and design limitations of a ‘combo’ wheel to ensure you choose the right wheel for the demands of your application.”
Combination wheels are good for specific market segments like mid-stream pipeline construction, pressure vessels and shipbuilding. One of the major specific applications in these markets is known as root pass or “bead” grinding.
“During the multi-pass weld process, the root pass is the first full weld laid,” Hufford says. “Welders or welder’s helpers grind the root (or bead) weld down to prep it for a hot pass and to ensure full penetration of that weld. We have measured the temperature of the root being ground right after the weld process to be up to 500 degrees F. At this temperature, most grinding wheels will glaze over as they are not designed to be exposed to that kind of heat.”
“A common practice is to ‘chip’ the edges of the wheel with a file or other tool to allow the wheel to continue to grind,” he continues. “We’ve developed a specific wheel that wears down as you are using it on hot welds so that it does not need to be chipped or altered.”
The Tiger Pipeline wheel eliminates the need to chip the wheel for aggression and it is safe for all vertical and angled applications. It also reduces chatter, stays in the bevel and is just the right thickness so it will not scar the bevel in multi-pass applications.